The biggest manufacturing trends impacting modular building manufacturers in the UK
5 min read | April 2025
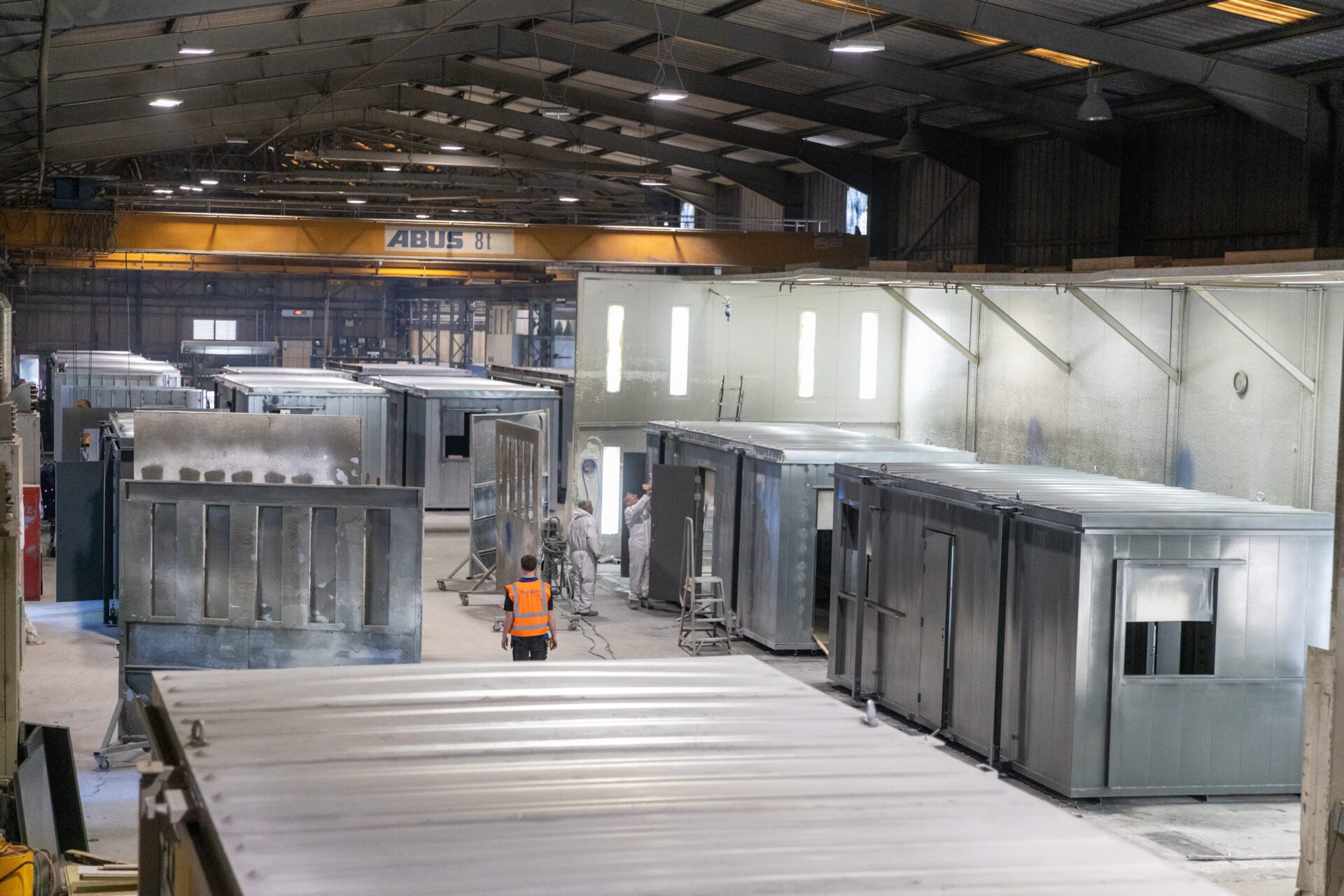
The manufacturing industry accounts for 8.6% of total UK economic output, and 8% of employment. With the industry constantly evolving to adapt to different manufacturing trends, we’ve been looking at what some of these trends mean for modular building manufacturers in the UK.
Below, our production director Dan Pollard, and our HR director, Liz Scott, share their thoughts on how skills shortages, supply chain management, sustainability mandates and more are impacting modular construction in the UK.
What are the biggest challenges facing the modular construction industry in 2025, and what are businesses doing to combat them?
“The UK construction industry has long faced a skills gap, and offsite manufacturing is no exception”, says Dan. “The shift towards factory-based production means workers need expertise in automation, digital design, and modular assembly, meaning recruiting workers with all those skills is difficult.”
Liz agrees, saying: “Skills shortages, particularly in trades such as welding, are having a big impact on ourselves and others in the modular construction industry. To combat this, we’ve been looking at partnering with colleges and apprenticeship providers to develop a pipeline of skilled workers.
“We’re big supporters of BetterWeld’s apprenticeship programme, which is empowering the next generation of skilled professionals through apprenticeships and training. It’s initiatives like this that help to inspire young people into offsite manufacturing, ensuring new talent can be continually developed.
“Beyond just attracting talent, employee retention is hugely important too. We’re making big efforts to ensure a culture where our team feel supported in their roles, whether that’s through one-to-ones or training courses to further themselves”, Liz continues.
“While construction and manufacturing are both often seen as male-dominated industries, as we move into the coming years we need to challenge these concepts and increase the visibility of women in roles across the business”, says Liz. “A diverse workforce will bring new, innovative ideas forward, and those in the modular construction industry should look to counter stereotypes by creating a welcoming and inclusive workplace culture.”
Outside of recruitment, Dan cites issues around supply chain disruptions and regulatory barriers as key challenges facing the offsite construction industry.
“The aftermath of Brexit, global inflation, and logistical challenges continues to put pressure on modular building manufacturers in the UK, affecting material availability and pricing,” says Dan. “Steel, timber, and insulation costs remain volatile, impacting modular manufacturers’ margins. In response, we’ve been strengthening local supplier networks, exploring alternative materials, and implementing lean manufacturing principles to minimise waste and improve efficiency.
“While offsite construction offers faster delivery, planning permission and building regulations can still delay projects”, Dan mentions. He notes that there’s a need for businesses to “engage with government bodies to push for standardised modular building regulations”, and “leverage digital twin technology and Building Information Modelling to ensure compliance before production begins.”
What are the biggest opportunities for modular building manufacturers UK in 2025?
Dan finds that meeting the demand for infrastructure as the biggest opportunity for modular building manufacturers in the UK, with a particular focus on the ability of offsite construction to lead on sustainability.
“There’s a growing demand for modular schools and hospitals, and the government’s plans for infrastructure investment over the next few years offers up great opportunities”, says Dan.
“One of the biggest opportunities for offsite construction is the rising demand for low-carbon buildings, in efforts to meet sustainability targets,” Dan notes. “Modular construction can reduce waste by up to 90% compared to traditional methods and often uses sustainable timber and recycled materials in production. With investors and developers prioritising green construction, there’s a real opportunity for modular firms to win more contracts.”
From a recruitment perspective Liz mentions that a “stronger focus on sustainable construction means that offsite construction can attract workers who are interested in learning about or utilising environmentally friendly building methods.
“The growing interest in apprenticeships also provides a great opportunity for the modular construction industry to strengthen ties with schools, colleges, and training providers, to bring in the next generation of talented workers.”ving created bespoke building solutions for sectors including commercial, healthcare, residential, education, construction and infrastructure for the past five decades.
How can the modular construction industry see more growth over the next year?
“The biggest areas for growth lie in leveraging technology, expanding manufacturing capacity, and strengthening industry collaboration”, says Dan.
“By investing in digital innovation and automation, modular building manufacturers can streamline the planning and production phases, whilst improving consistency and reducing waste. Simultaneously, establishing new production facilities will enable firms to meet the growing demand for new infrastructure, whilst scaling supply partnerships will ensure a steady material flow to hit requirements”, he adds.
“Across the industry, collaboration is hugely important. Strong relationships between developers, local authorities, and policymakers are needed to promote modular construction as a mainstream method of building”, Dan continues.
“It’s only then that we’ll be able to enhance the public’s awareness and confidence in offsite construction, addressing misconceptions and highlighting the cost and energy savings for homebuyers and businesses.”
Dan concludes by stating: “While 2025 presents challenges for the offsite construction sector, it also offers unprecedented opportunities for growth and innovation.
“By leveraging technology, improving supply chains, and working collaboratively, modular manufacturing can drive the future of UK construction, offering faster, greener, and smarter building solutions.
“The modular building manufacturers in the UK that embrace these strategies will be best positioned for success in the evolving market.”
Read our Other Recent News
Foxford School chooses Thurston Group to deliver off-site manufactured classrooms
Thurston Group is set to deliver a full turnkey solution for additional classrooms at Foxford School & Community Arts College in Coventry.
6 min read | Matt Goff
Championing women in construction: how to Accelerate Action this International Women’s Day
At Thurston Group, we believe it’s important to champion women in construction. Our team has been discussing the challenges and rewards of working in the industry.
6 min read | Liz Scott